Spreading the risk
There’s no rule book on the Taggarts’ farm in North Canterbury, and they don’t mind the debt because it keeps them pushing. Story and photos by Annabelle Latz.
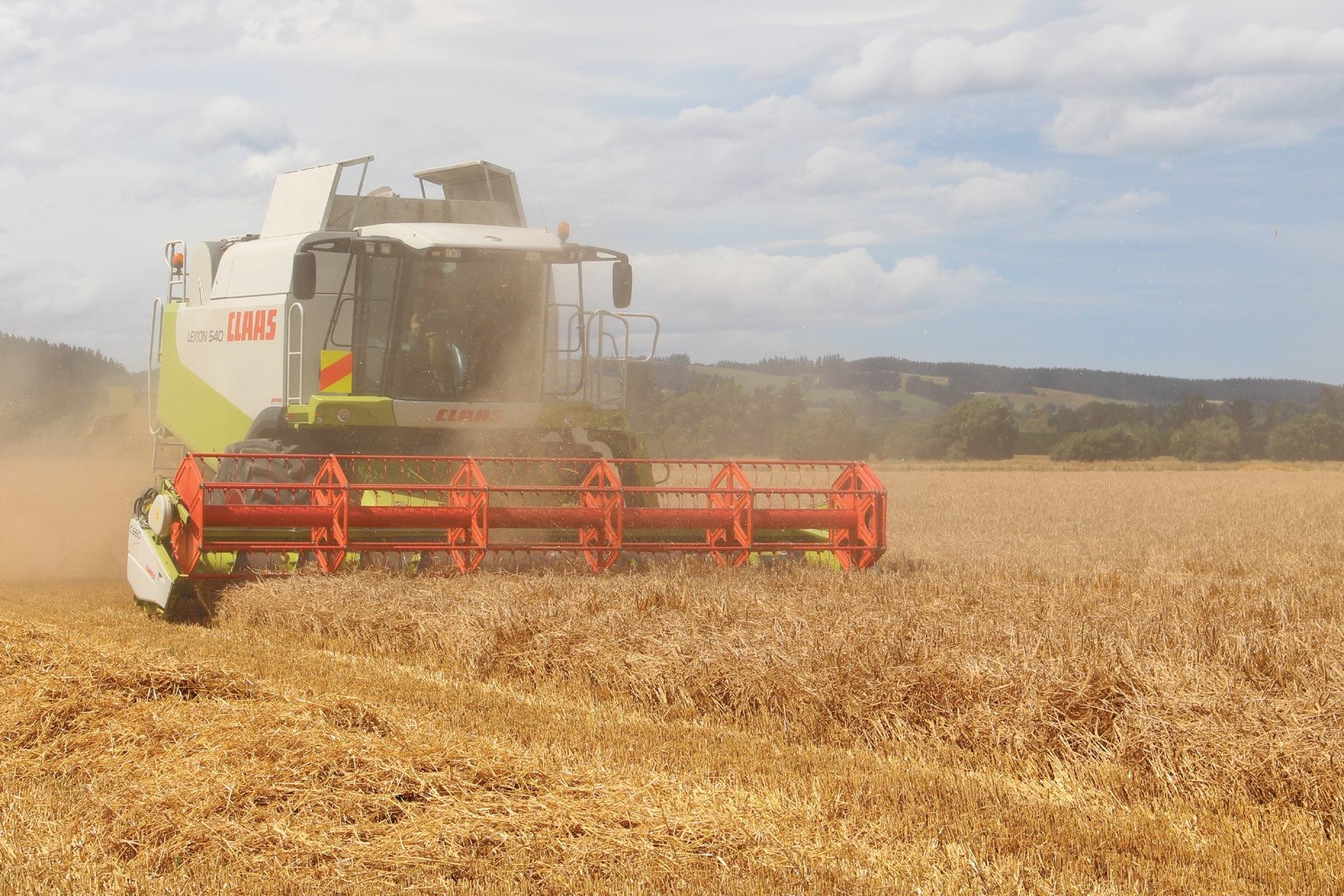
A stone’s throw from the quiet rural town of Cust, the 732-hectare (714 effective) mixed-cropping farm sits in behind Summerhill, where to the west are the Southern Alps, and to the south across the Waimakariri River are the Canterbury Plains.
The Taggart family has worked this land since 1958, now three generations deep.
“We are having a big consolidation now,” Roscoe says.
Having the ability to diversify is key to help spread the risk. During any year there will be fluctuations of lambs on the ground, crop production and in how they’re utilising the residues.
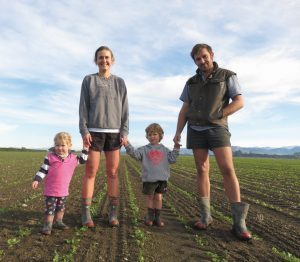
“Our strength is that we are able to diversify with our crops, tonnages, and animals.”
The income blanket has been thrown wide over various income streams and markets, to hedge any major downturns and not make themselves too reliant on one area.
“We have got an absolute mountain of debt, we are doing this to save money because we can’t afford to take punts.”
Rainfall used to average about 650mm a year, but in recent years it’s been closer to 700mm. Roscoe would choose to irrigate over a muddy summer, reflecting on the previous two harvests that have been the worst in 20 years.
“Rain equals disease, which means a lot more spraying.”
Every hectare must pay its way, because each one they paid for, therefore must provide a return.
Roscoe, his wife Gracie and Roscoe’s father Murray, who is the Alliance Meat Group chairman, work in a trading partnership called Taggart Farms, leasing the four family farms.
Roscoe bought his own first bit of dirt in 2012, and since then has been adding to it.
“If more land comes up, we’ll buy it or lease it, because I love the idea of growing the farm.”
Farm and family life is busy. Roscoe and Gracie have three children, Harry 3, Heidi, 2, and Ollie, 6 months.
The farm comprises two full-time staff, a truck driver for six months of the year, and Murray works on average one or two days a week, Gracie helps when she can, and they call on a part-timer when needed.
Sitting between 160m and 180m above sea level, the soils are a mix of Pahau, Damley, Wakanui, Claremont, Balmoral and 100ha of peat which they put drainage through.
“The range of soil types gives us flexibility around crop rotations,” Roscoe says.
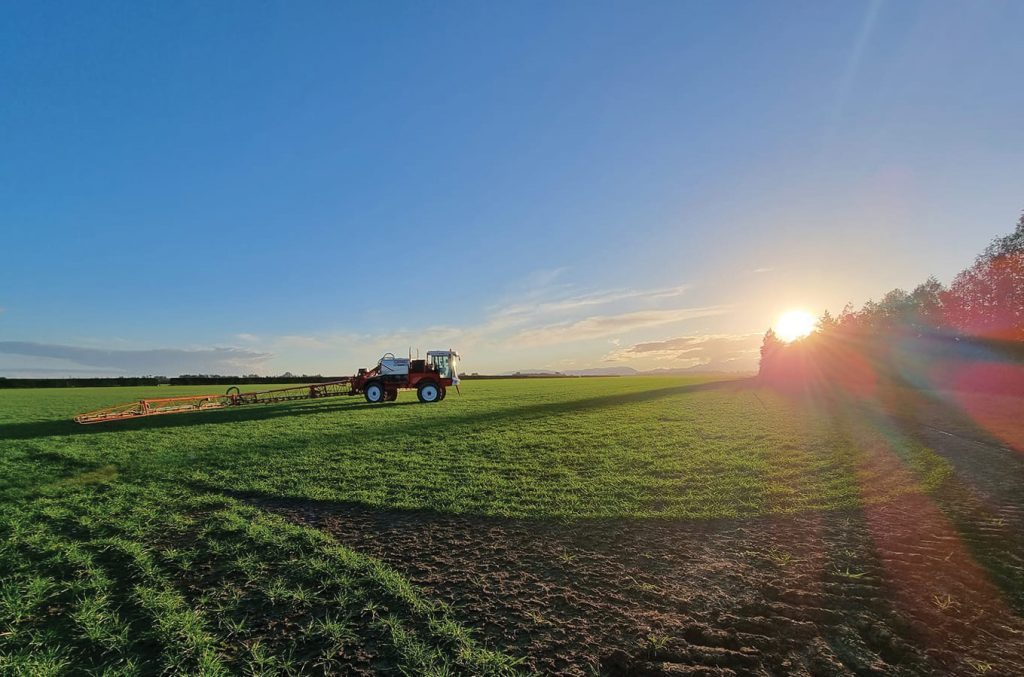
Crop and stock integrate well
They grow 220ha of wheat for the pig and poultry market. They have 175ha of ryegrass, 30ha of maize, 13ha of barley, with the balance made up of break crops for the export vegetable seed market – maize, forage rape, hybrid rape, carrots, parsnips, white clover, red beet, radish, corn salad, kale for seed, and a small patch for onion that they’re trialing.
They have roughly 2500 tonnes (t) of wheat storage, which Roscoe admits is not enough, so they try to deliver as much crop as possible straight off the combine or out of the dryer to make sure everything can fit.
They do their own trucking.
This is the first year they’ve grown maize, earmarked for the grain market. This works in well with the cull cows, as once the grain is harvested, the cows graze the residue supplemented with balage, which adds to the gross margin.
“It’s a nice environment having 250 cows grazing over 15 hectares,” Roscoe says, adding that choosing the grain market over making silage also has its environmental benefits. About 300 units of potassium comes off the paddock making silage compared to 80 units for grain.
The record wheat yield is 15t/ha; their worst has been 4t/ha, put down to seasonal changes, availability of irrigation, bad yields are the general nature of dryland paddocks.
Ryegrass sits about 1600kg/2t, white clover comes in between 500–800kg/ha.
The benchmark net profit over the farm is always $3000/ha.
White clover is a good option at the moment, making up 85ha of their crop farm; it used to be 30ha.
This is due to a couple of bad clover harvesting years which has maintained high prices, complemented with low-input requirements for chemical and fertiliser. Roscoe said all the clovers have different prices and cost structures, but overall white clover exceeds their benchmark comfortably,
Like any business, gross margin is the biggest factor, but minimal spray and fertiliser is significant too.
Grass grub and slugs mean a need to cultivate, and grass weeds are always an issue.
To name a few, blind seed disease, rust, BYDV, fusarium and septoria can pose challenges.
With the vegetable seeds, on average they reach their targets, which are estimated yields from the agronomist. Roscoe holds huge value in the four agronomists he draws expertise from and who he’s stuck with through both the good times and the more challenging ones.
“I’m a big fan of relationships.”
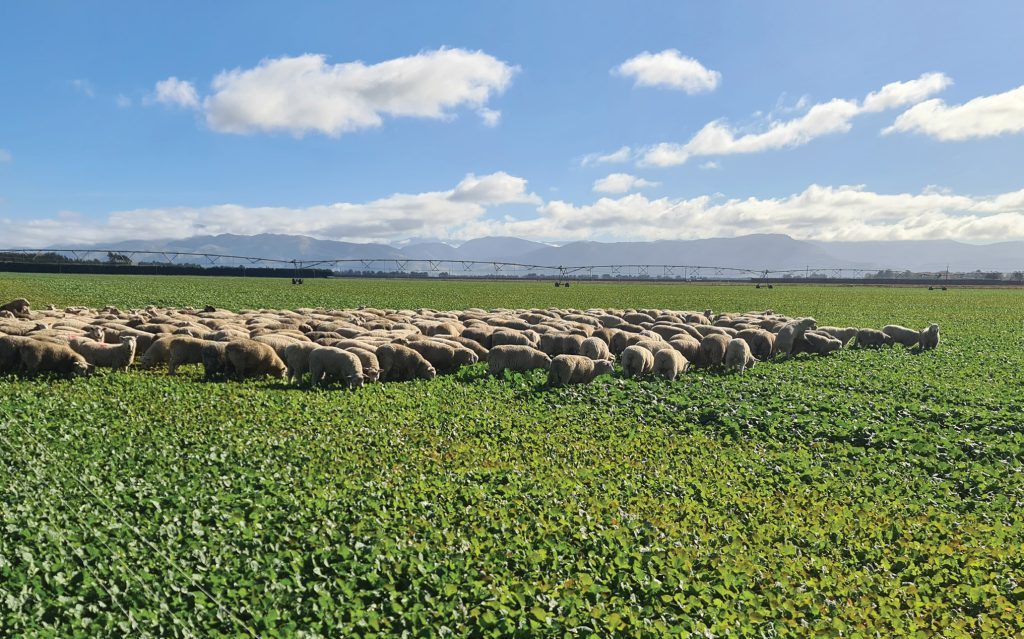
The overall picture
On the irrigated land, the five-year rotation rolls by with autumn planting in April and May made up of wheat, autumn break crop, wheat, ryegrass, spring break crop, then back to wheat. The dryland rotation is ryegrass, forage rape for lambs, wheat, then into ryegrass again.
Winter means maintenance, fencing, and also fattening lambs. Each year they finish about 5500 which arrive in February and March. They’re a mix of Romney Texel-cross and Merino cross, with a preference for anything with a black face.
They winter lambs on pasture that is ex-ryegrass and rape sown for forage, direct drilled into areas of the farm that sit on riverbed. Lambs also graze the dryland cropping areas.
Spring is about spraying and fertilising for crop maintenance. The lambs are sent to the works in October – they aim for a $40/head margin. In years gone by, lamb numbers have been as high as 8000, but at the moment it’s better to use that land for crops.
Spreading and spraying happens from August through to early December and spring planting is August to October.
Shifting irrigators keeps things busy late September until late January or early February, depending on the season.
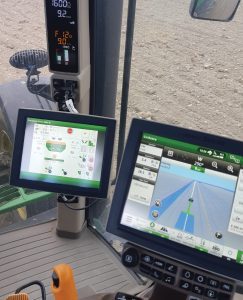
“We look at every paddock and ask ourselves, what is the best way to use it?”
They cultivate and drill, depending on the season, what they are growing, disease and insect pressure, water usage, and establishment cost.
“Everything is situational. As soon as you stick to one rule, you hamstring yourself.”
Applying precision technology
To ease their reliance on contractors, five years ago the Taggarts bought their own spreader. At the time, the extra cost to buy precision technology was only marginal, requiring minimal additional yield or savings on fertiliser to cover its costs.
“The GPS mapping provides georeferencing and spread maps, while the N sensor does the sensing and rate control,” Roscoe says.
As the spreader goes through the paddock, chlorophyll levels of the plants are sensed using infrared and the normalised difference vegetative index (NDVI) to calculate crop health, while nitrogen (N) sensors attached to the tractor’s roof dictate the rate to the spreader.
“At the beginning it was difficult to trust the technology, but it has paid off.”
For the first three seasons they used standard variable rate based on satellite imagery for their N application. For the last two seasons they’ve used variable rate, based on an N sensor map.
They also use the sensor over brassica, maize, barley, and ryegrass as well as the wheat.
They used to apply N based on the FAR recommendation of 25 units of N/t of grain produced, but they have got that down to 20 units on average.
“Five units of N/t of wheat produced over 2500t is 10,000 units, which is just over 27t of N fertiliser, just on our wheat.”
Information about growth stage, expected yield and rate parameters are dialled into the system for N application, and the maps can be used for variable rate spraying and planting.
For irrigation they use two pivots with variable rate irrigation (VRI) on one of them, linears, and one roto rainer (which they want to get rid of).
“The VRI water based on an electromagnetic map means that different soil types get different rates of water to minimise excess water usage or nutrient loss.”
This irrigator is coupled with a 6ha water storage pond that acts as a buffer for the irrigator, increasing the irrigation scheme water use efficiency.
The VRI pivot uses maximum 72 litres/second and minimum 23L/s, depending on what soil types it’s on.
Across the different on-farm activities, variable rate technology is used on more than 670ha of the farm on ryegrass, brassica crops and barley.
Due to the scale it’s used, the Taggarts managed a 100% return on capital on the N sensor.
“We will always aim to have debt behind us – it means we have incentive to push things, and it creates pressure to keep us moving.”
Environmental and economic factors are considered when deciding what crops need fewer inputs. Roscoe says they’ve got better at growing their 30ha of peas, with a cost about $1100/ha which can vary based on the season.
“Gross margin is still key at the end of the day.”
They map for soil testing and are now in their second year of grid sampling. The variability of trace elements they discovered means across the paddock they may apply 0.5t/ha of triple super at one end and half that at the other.
“There is insane variation across the farm. A paddock that is dead-flat has way more variation than you’d think, taking in an old gravel pit, history of sowing, stock and soil types.”
As with all trace elements, quite often there will only be small areas of paddocks they are actually spreading on.
“Generally about the same money is spent per hectare, due to using more expensive products plus the cost of sampling, but we know everything is going in the right place.”
They grid map quarter of the farm each year, and then after year four they’ll start again.
“Blanket fertiliser application is not an option anymore, we’ll never go back to using a base-rate system again.”
Tight on capacity
Their combine harvester, a Claas Lexion 540 clicks over 400 hours a year. Ideally it needs to be replaced, but in the economic climate they make do and look after what they have.
“There’s no capacity to replace just for the sake of a ‘nice to have’.”
The main work comes from their two John Deere tractors, 230 HP, and a 130 HP that’s completed more than 10,000 hours. They also have a 36-metre boom sprayer.
Roscoe admits they’re a bit tight on capacity and could do with a bit more horsepower behind them.
“We are looking very hard at the machinery we use. But if we’re getting the productivity and yield we’re after, we’re good with what we’ve got. We’re trying to make the farm profitable, so that’s the sacrifice.”
In five years the aim is to have machinery up to date for the scale of the farm and to continue on with precision technology. Solar is a great idea, but for now it sits in the nice-to-do, although Roscoe says it’s a great way to make a return on a shed roof.
If something hasn’t been used for three years, they sell it, because “being neat and tidy pays dividends”.
Holding paddocks around yards are as small as possible. “It’s about maximising every area.”
A young family means adventure activities like jet boating and mountain biking are on the back burner for now. Time off the farm is still of big value whether it be enjoying local North Canterbury holiday spots, or heading to Gracie’s family farm near Hawarden, North Canterbury.
“Farming is not a job, it’s a lifestyle we absolutely love and we can incorporate the whole family.”