James Hoban has built a new woolshed on his Marlborough farm. He outlines how they went about this once-in-a-generation project, why they did it and what worked well.
After a lot of cursing and dreaming, 2021 saw us shearing in a brand-new woolshed. After three years of planning and two main shears in a new woolshed we are happy with what we created.
Our old woolshed was not purpose-built but was rather a set of century-old stables converted for the job. A concrete block wool room had been added but the chaff chute remained in the loft, over the gratings.
Despite a sticker proclaiming borer treatment in the 1960s, holes in the timber were abundant. A shaft drive plant was still in operation and shearers were too close together. There was storage for 300 sheep maximum for the three-stand shed and catching pens only held seven woolly ewes. Getting them into the catching pens involved pushing them up a 400mm-wide ramp, directly towards the shearing noise. Penning during crutching was a full-time job.
The state of the old woolshed made a newbuild or a major overhaul a necessity. Even if we were dealing with crossbred wool we would have needed to take drastic action. After much circling it became obvious that a major overhaul of the existing shed would still rack up massive costs. The limitations of the sloping site and existing building were daunting.
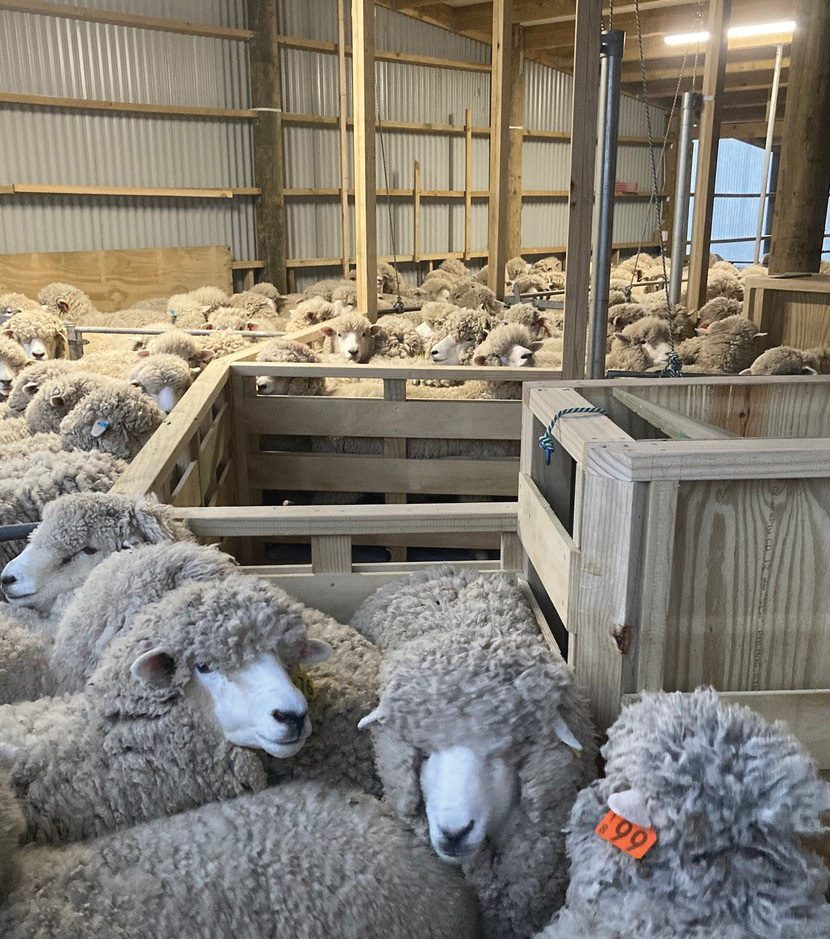
Doing our homework
Once we decided we were definitely in for a new shed rather than trying to polish an old eyesore, we researched our options.
Cost was always going to be a major consideration. Quotes from four different shed companies showed a $100,000 variation on a budget of $250,000. The expensive options were from well-known, widely used companies. There was also a difference in the expertise companies could offer.
We opted for Greenwood and even in hindsight it was the right decision. They were experienced with woolsheds and took time to understand any intricacies to suit our needs. The quality of materials and timeliness of deliveries were excellent.
They were not the cheapest of the four quotes but were competitive and could offer a better service and deeper understanding of our project than the company that beat them on price. Taking the cheapest quote would have created subsequent headaches.
We spoke to shearers, wool handlers and other farmers before deciding on our final design. We asked our local contractor, who had worked in a lot of different sheds and had done his fair share of penning up, which sheds flowed the best. He recommended a local shed which, while older, was a breeze for penning up and worked well.
We visited this shed when it was in use and modelled our pens off it and another newer version we knew well. Seeing sheep running was important but a follow-up visit with a notebook, tape measure and plenty of time, when the shed was not in use, was also key.
The pen design is reasonably common and the keys for it working are that pens are side loading, each catching pen has a filling pen the same size and sheep are never being pushed directly towards the noise of the machines or music. A horseshoe board was required to make the pen setup possible.
We also had two shearing contractors inspect the shed once we thought it was finished to see if we had missed any details. This resulted in some minor additions, such as chains on the ceiling to attach back-support cradles, which went a long way. Shearer feedback has all been positive.
Flat board vs raised board
One of the most common questions people ask when we talk about our new shed is why on earth would we opt for a flat board over a raised board.
After 70 plus years working with wool, my father initially asked the same question. He began working in an ancient shed where sheep were penned overnight, then let out in the morning before condensation began dripping off the ceiling, then gradually fed back inside for shearing. He graduated to a two-story shed which he built with his father in 1963 and which was a major breakthrough for them.
Raised boards were an innovation about the time that shed was built and only starting to make an entrance so to keep things simple they stuck with a flat board. Fifty years and more than 100,000 fleeces later Dad was fairly certain if he ever built a new shed it would have a back-saving raised board.
Then we started talking to shedhands and other farmers who had built new sheds. Shearers we asked were ambivalent as long as there was enough space to shear. Shedhands were split but most favoured a flat board and commented that only the lazy ones would want it raised. Interestingly the shed hands who we considered to be the best at their job wanted a flat board.
In addition we spoke to several fine wool growers and reached the conclusion that a flat board would mean better quality wool preparation – something reinforced by the better shedhands. The comment was made many times that a raised board would be fine for crossbred wool but with finer wool a flat board was a better option.
A flat board has created a better space in the wool room, allowed us to have a lower shed and simplified the building process. We put 300 rams through the shed annually and do not sedate them for shearing. Longer-term, we think there might be a safety issue working with big rams, without sedation, on raised boards.
Grating options occupied a lot of time, discussion, woolshed visits and deep thought over several years. We opted for three different types. The grey fibreglass catwalk type sheets are Graycol composite grating which is imported to Christchurch from China. There can be a significant wait time so it had to be ordered early. Graycol, steel mesh and timber grating were all reasonably close in price. Graycol grating had the benefits of being quick to install and reasonably light to handle. It also seems to be quieter than steel mesh.
Greenwood’s timber grating was excellent quality and was used for the catching pens. Grating in catching pens has to be laid longways so that sheep are dragged along it rather than across it. This stops sheep getting traction with their feet in the gaps and pushing back when being dragged out on to the board.
Our shearers have told us it is surprising how often new grating is installed the wrong way around. The Graycol grating would not be ideal for sitting sheep down on and dragging them over but works well in the other pens.
Under the wool room we have dry storage for sheep on green plastic grating that came from decommissioned sheep milking barns near Invercargill. This was by far the cheapest grating we found and has worked well but it was not for sale when we ordered the other grating. It clicks together like a jigsaw, in sheets about 0.3 square metres.
Keeping costs manageable
We were extremely fortunate to have a recently retired builder in the family. Ross McEwan came up from Te Anau and did all of the internal aspects of the shed. Local builder Les Webb built the shed shell, loading area, ramps and stairs.
We built our own yards and all the gates for the woolshed pens. Having a father who would have been a builder if he had not gone farming was also a major benefit. Our children were used at every opportunity and their pay remains a grey area.
A quality family weekend saw more than 100 sheets of ply painted white, twice, to line the ceiling and improve lighting. Jack Russell footprints are still visible on some of those sheets. All of these things meant we kept costs manageable. We were also fortunate with timing in that the materials were ordered and paid for before the massive hikes in building costs.
The bank was supportive of the new shed for three main reasons. First, everyone understood when we came to this property five years ago that it needed to be in the budget. Secondly, we did not get carried away on an over-the-top shed and minimised costs where we could. Realistically the shed we have built would cater for a much bigger ewe flock so has future-proofed the business if it grows. Thirdly, we made it a multi-purpose shed, including covered yards. The final cost was $254,000.
As well as being a wet weather basketball venue to send the kids to, it is our annual ram sale venue and we use it for stud sheep work at various times. We know of other farmers who have carried out major tractor engine overhauls in their woolsheds but we did not go that far.